- HOME
- コラム
- プラント・工場施設検査
- 予防保全について、他の保全方法と比較しながらメリットデメリットを徹底解説!
予防保全の詳細情報と実践法
予防保全とは、設備や機器の故障に先回りして、定期的な点検・メンテナンスを実施することにより、突発的なトラブルの発生を防ぐことを目的とする手法です。故障が起きてから対処するのではなく、壊れる前に手を打つことで、生産ラインのダウンタイムを最小化し、企業活動を円滑に進めることが可能になります。
例えば製造業では、メインの生産設備が突然停止すると納期遅延を招き、顧客に迷惑をかけるだけでなく、企業の信用を損なうリスクが生じます。また、ITサービス業界においても、サーバーが障害を起こすと利用者へのサービスが止まり、ビジネス機会の損失やブランドイメージの低下につながります。
こうした背景から、予防保全は多くの業種・業界で注目されるようになりました。加えて、近年ではIoT技術やAI解析の進化により、機器の状態をリアルタイムで把握できるようになり、高度な保全計画を立案しやすくなっています。以下では、予防保全及び設備保全の概要や保全業務の具体的手法、他の保全手法との違い、さらに実践事例などを詳しく解説していきます。
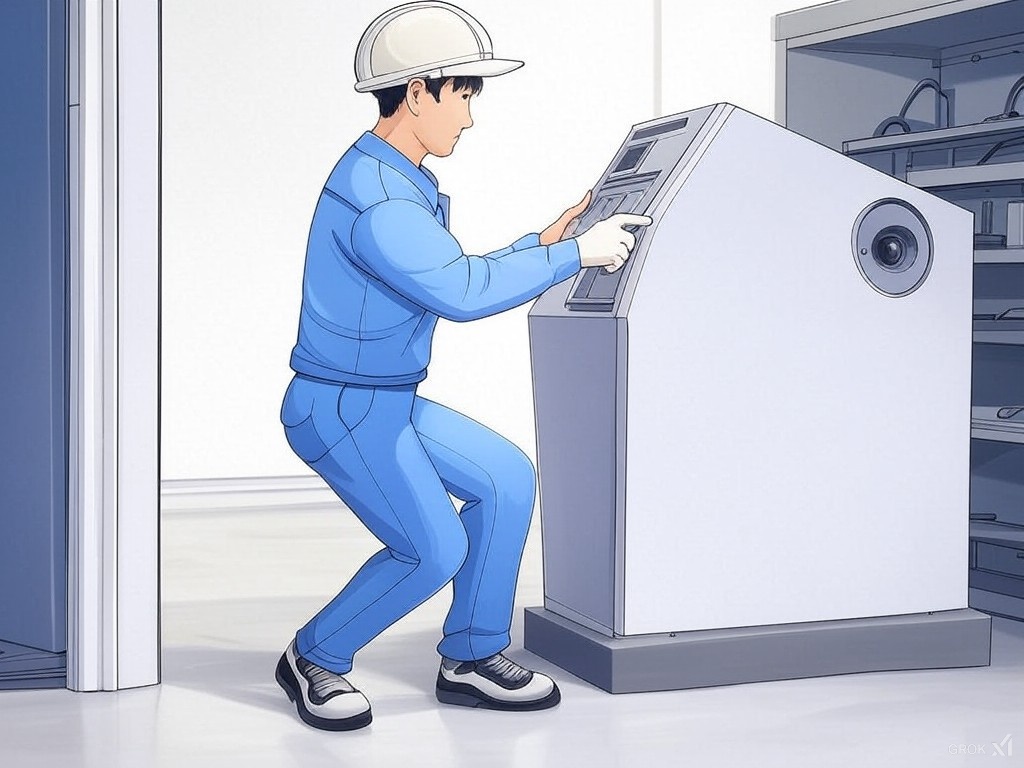
予防保全とは
1-1. 故障リスクの最小化
予防保全の大きな目的は、故障リスクを未然に防ぎ、安定的な稼働状況を確保することです。設備が突発的に停止すると、修理費用や生産ラインの停止コスト、人的リソースの投入など、様々な負担が一度に発生します。特に24時間365日稼働を要する産業では、生産停止が企業の損益に大きく影響するため、事前に保全活動を行う意義は非常に高いといえます。
1-2. ロングスパンでのコスト削減
一見すると、頻繁なメンテナンスはコストがかかるように思えますが、長期的なスパンで見れば、事前対策に投資するほうが総費用を抑えられるケースが多いです。故障箇所が大きくなると修理費も上がり、最悪の場合は設備の交換を余儀なくされる場合もあります。適切なタイミングでの部品交換や調整を実施することで、結果的にトータルコストの最適化が図れます。
1-3. 品質と信頼性の向上
設備トラブルが頻発する職場では、製品品質のばらつきや従業員のモチベーション低下を招く可能性があります。逆に、予防保全が行き届いた職場では、安定した生産・サービス提供が可能となり、企業イメージや顧客満足度の向上に寄与します。このように、予防保全は企業の競争力強化という観点でも非常に重要です。
予防保全の主な手法
予防保全には、多様な切り口・考え方があります。ここでは主に5つの代表的な手法を取り上げ、それぞれの特徴を解説します。
2-1. 定期保全(時間基準保全)
あらかじめ設定した時間や周期に基づいてメンテナンスを行う方式です。例えば「稼働から3ヶ月ごとに一斉点検を実施」「週に一度は外観検査を行い、油脂類を補充する」など、スケジュールを明確にして運用します。
- メリット
- 作業スケジュールが立てやすい
- 専門知識の少ない現場でも導入しやすい
- 短期的な運用が比較的簡単
- デメリット
- 設備の実稼働状況を考慮しないため、過剰メンテナンスの可能性がある
- 稼働時間が少ない機器でも一定のサイクルで点検するため、コスト面が不利になる場合がある
2-2. 利用基準保全
設備の使用頻度や稼働時間、あるいは負荷状況を基準にして保全タイミングを決定する手法です。例えば「1000時間稼働するとオイルを交換」「負荷が一定量を超えたら点検する」といった形で運用します。
- メリット
- 設備の稼働状況に合わせたメンテナンスが可能
- 部品の交換時期を最適化し、無駄なコストを削減できる
- デメリット
- 稼働データの取得や分析が必須
- 正確な利用状況の管理・記録がないと、最適なタイミングを逸するリスクがある
2-3. 状態基準保全
センサーや監視装置を用いて、設備の現状(状態)を常時モニタリングする手法です。温度・振動・音など、多角的なデータを収集・解析することで、異常兆候を早期発見し、適切な時期に修繕を行います。
- メリット
- リアルタイムで状態を把握でき、突発故障を予防しやすい
- ダウンタイムを最小限に抑えられる可能性が高い
- デメリット
- センサー導入やデータ管理などの初期投資が大きい
- 解析環境(ソフトウェア・人材)の整備が必要で、運用ハードルが上がる
2-4. 予知保全
AIや機械学習、ビッグデータ解析を活用して将来の故障を予測し、最適なタイミングでメンテナンスを行う手法です。設備の各種履歴データを解析し、異常発生の前触れや周期を推定します。
- メリット
- 故障の予兆を高精度で捉えられるため、緊急停止を回避しやすい
- 生産効率を落とさず、費用対効果を最大化しやすい
- デメリット
- 高度なAIシステムの構築・維持に莫大なコストが必要
- データの質や量によって予測精度が左右される
2-5. 故障発見保全
定期点検に際して、潜在的な故障や不具合を早期に“発見”して修理する手法です。予め決められた点検項目を詳細にチェックし、異常の兆しがないかを確認します。
- メリット
- 大規模な監視システムがなくても導入しやすい
- 設備ごとに専門知識を持つ保全員が対応するため、細かな不具合にも気づきやすい
- デメリット
- 点検の実施タイミングによっては故障リスクを完全に防ぎきれない
- 点検作業自体に工数を要するため、生産効率が一時的に下がる可能性がある
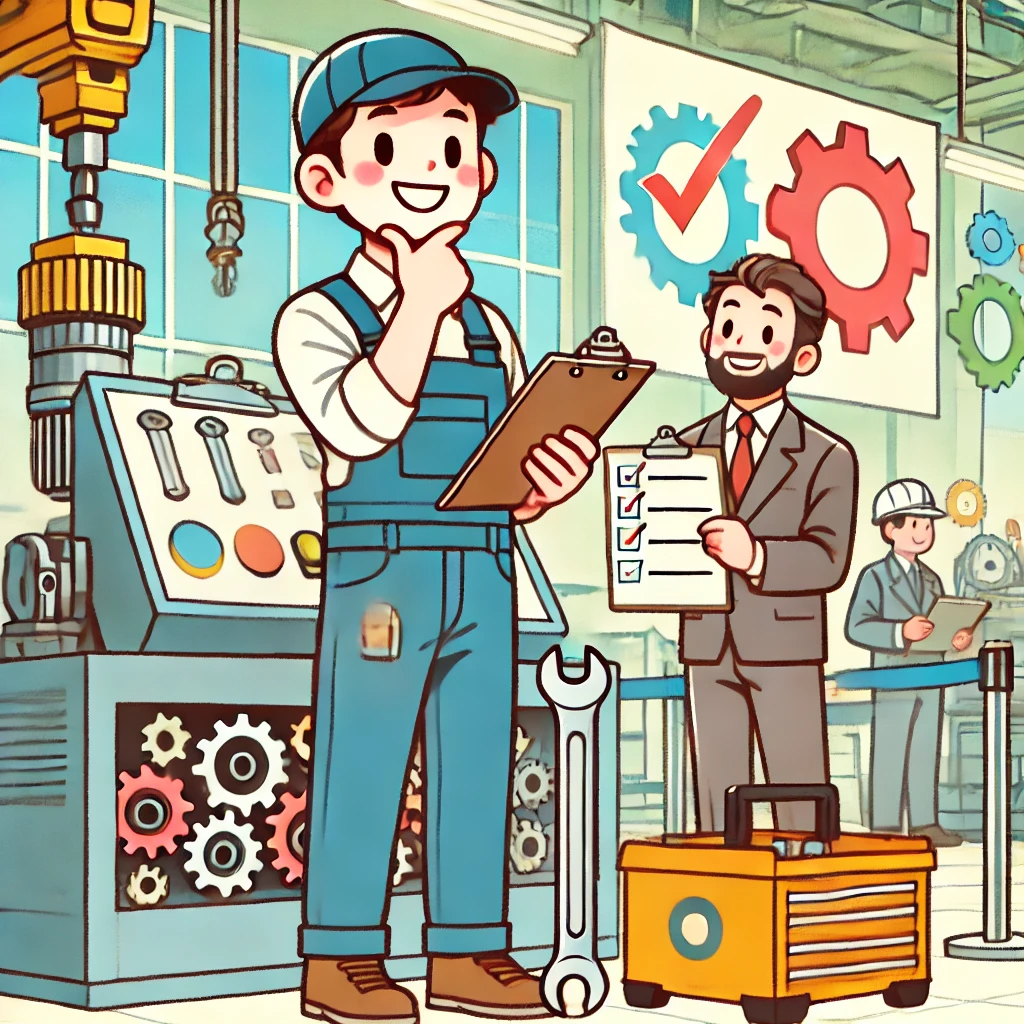
予防保全と他の保全の違い
予防保全と他の保全手法の違いを理解することは、設備管理において重要な要素です。違いを理解し、効果的な保全手法を選択することで、設備の安定稼働を実現し、企業の生産性を向上させることが可能です。
3-1.事後保全(突発保全)
手法概要
設備が実際に故障してから修理・部品交換を行う手法です。平時は特に大きなメンテナンスコストをかけずに済む反面、故障が起こると生産停止や納期遅延のリスクが高まります。
- メリット
- 平常時のコストが低い
事前に点検や部品交換を行わないため、通常運転時には余計な費用がかかりません。 - 運用がシンプル
「壊れるまで使う」スタイルのため、特別なスケジュール管理やデータ管理を必要としません。
- 平常時のコストが低い
- デメリット
- 故障時の損失が大きくなりやすい
設備停止による生産ロスや急な修理費用、部品の納期遅延などが一度に発生します。 - 安全面のリスク
重大な故障や事故が発生しやすく、高い信頼性・安全性が要求される設備には不向きです。
- 故障時の損失が大きくなりやすい
- 予防保全との違い
- 事後保全は「故障後に修理する」のが基本ですが、予防保全は「故障が起きる前に計画的に防ぐ」ことを重視します。
- 事後保全では、短期的な運用コストは抑えられる一方、故障が起きると高額な修理費や生産停止の損失が発生するリスクが大きくなります。
3-2. 修繕保全
手法概要
設備に軽微な異常の兆候(動作音の変化や振動の増加など)が見られた段階で修理や部品交換を検討する手法です。事後保全ほど放置はしないものの、異常が起きてから対応する点が特徴です。
- メリット
- 比較的早めの対処が可能
完全に壊れる前に修理に着手するため、大きなトラブルに発展する前に被害を抑えられる場合があります。 - 過剰メンテナンスを抑制
あくまで異常が出てから対応するため、予防保全ほど頻繁に部品交換をしなくて済むケースもあります。
- 比較的早めの対処が可能
- デメリット
- 異常を見落とすリスク
兆候が分かりづらい設備の場合、結果的に突然の故障につながる可能性があります。 - 恒常的なモニタリングが必要
軽微な変化に気づくための知見や観察体制、計測ツールなどを準備しておかないと、対処が遅れることがあります。
- 異常を見落とすリスク
- 予防保全との違い
- 修繕保全は「軽微な異常が発生してから修理」を行う手法で、異常が顕在化していることが前提です。
- 予防保全は、異常が生じる前の段階から点検や交換を予定しているため、より早いタイミングで故障リスクを抑えることができます。
3-3. 計画保全
手法概要
設備のライフサイクル全体を見据え、中長期的な視点で「どの設備に、いつ、どれだけの投資や人員を配分してメンテナンスするか」を計画的に管理する枠組みです。企業全体の設備投資計画や生産スケジュールと連動させることが多いです。
- メリット
- 大局的な運用が可能
設備更新や増設のスケジュールも含め、全体最適化を図れるため、突発的なトラブルに左右されにくい。 - 経営戦略との整合性が取りやすい
企業のビジョンや生産拡大計画と連携し、必要なタイミングで最新設備の導入や既存設備の改修を行いやすい。
- 大局的な運用が可能
- デメリット
- 運用管理が複雑化
大規模な工場や、多種多様な設備が混在している現場では、計画策定とスケジュール調整に手間がかかる。 - 柔軟性に乏しい場合がある
あらかじめ長期計画を組んでいるため、技術革新や需要の変動に対して迅速に対応しづらい面もある。
- 運用管理が複雑化
- 予防保全との違い
- 計画保全は、設備更新や大規模投資を含めた長期的な全体マネジメントの一環として、メンテナンスの時期・予算を策定する考え方です。
- 予防保全は、日常的・定期的に故障を未然に防ぐための個々の点検・修繕活動を指すもので、計画保全の中で具体的に実施される手段の一つといえます。
- 事後保全(突発保全)は、設備故障後に対処する手法で、平時コストは低いものの、故障時の損失リスクが大きい。
- 修繕保全は、軽微な異常の兆候が表れてから動くため、事後保全より早いが、明確な異常を見逃すリスクがある。
- 計画保全は、設備投資や長期的な生産計画も含めた包括的な保全マネジメントの考え方であり、企業全体の視点から最適なタイミング・方法を探る。
これらと比較すると、予防保全は「異常が表面化する前」に対応を行う点が最大の特徴です。長期的な視点で見れば、予期せぬダウンタイムの削減や安全性・品質維持に強みを発揮するため、設備の重要度や業種によっては非常に有効な手段となります。
予防保全のメリット
4-1. 突発故障の防止による生産性向上
- ダウンタイムの大幅削減
定期的な点検を行うことで、部品の摩耗や異常兆候を早めに察知し、故障が本格化する前に適切な対処を実施できます。結果として、設備の停止時間(ダウンタイム)が減少し、稼働率が高まります。 - 生産計画の安定性
ダウンタイムが短縮されることで、生産計画を正確に組みやすくなります。特に受注生産やタイトな納期が求められる業種では、突発的な故障が減ることが納期遅延の防止につながり、顧客満足度の維持にも寄与します。 - ライン全体への波及効果
メインの設備が停止すると、その設備に依存する前後の工程もストップするリスクがあります。予防保全によりキーマシンが安定稼働することで、関連工程まで含めた生産性が底上げされます。
4-2. 長期的なコスト削減
- 緊急修理費の回避
突然の故障は、緊急修理や部品手配が必要になるため、定価以上の費用が発生したり、輸送費が余計にかかったりするケースがあります。予防保全では計画的に調達・交換を行うため、コストの平準化と抑制が見込めます。 - 生産ロスの低減
設備が長時間停止すると、売上機会の損失や顧客への賠償リスクが生じる場合もあります。予防保全によって故障を防ぐことで、こうした想定外のコスト増を回避できます。 - 設備寿命の延長
適切な時期に部品交換やクリーニングなどを行うと、設備自体の寿命が長くなる傾向があります。結果として、設備更新のサイクルが延び、更新投資の負担が軽減されます。
4-3. 品質の安定と向上
- 一定水準の製品品質を確保
設備の稼働状態が常に良好であれば、製品品質のばらつきが減り、不良率を抑えられます。業種によっては微妙な動作の違いが製品精度や安全性に影響を与えるため、設備不調の早期発見は非常に重要です。 - 顧客満足度・ブランド価値向上
安定した品質の製品を継続的に提供することで、取引先や消費者からの信頼が高まり、自社ブランドの評判向上に直結します。 - トレーサビリティの強化
予防保全の一環で収集した稼働データや点検履歴は、万一の不具合発生時にも早期原因追究に役立ちます。品質管理体制の改善や顧客対応のスピードアップにつながります。
4-4. 在庫管理の効率化
- 交換部品の必要時期が明確化
定期的な点検データを分析することで、「どのタイミングで、どの部品を交換すべきか」がより正確にわかります。これにより、不要な在庫を大量に抱えるリスクが低減します。 - 適正在庫レベルの維持
交換部品を計画的に発注できるようになるため、過剰在庫だけでなく在庫不足による生産停止リスクも抑えられます。最適な在庫回転率を維持することで、在庫管理コストの削減に直結します。 - 部品サプライチェーンとの連携
製造メーカーや物流業者との連携を強化しやすくなり、必要な部品を必要なときに確保するためのスケジューリングが容易になります。
4-5. 従業員の安全確保
コンプライアンス・法的リスクの回避
労働安全衛生法などの関連法規に適合した保全体制が築けるため、設備トラブルによる法的リスクや社会的信用の失墜を防ぐことができます。
突発的な機械事故の防止
突然の故障は、オペレーターや周辺作業者の怪我・重大事故につながる危険性をはらんでいます。定期的な点検で異常を早期発見することで、安全リスクを大幅に低減できます。
心理的安心感の向上
設備トラブルが少ない職場では、作業者が不安なく業務に集中でき、士気向上やモチベーション維持にもつながります。
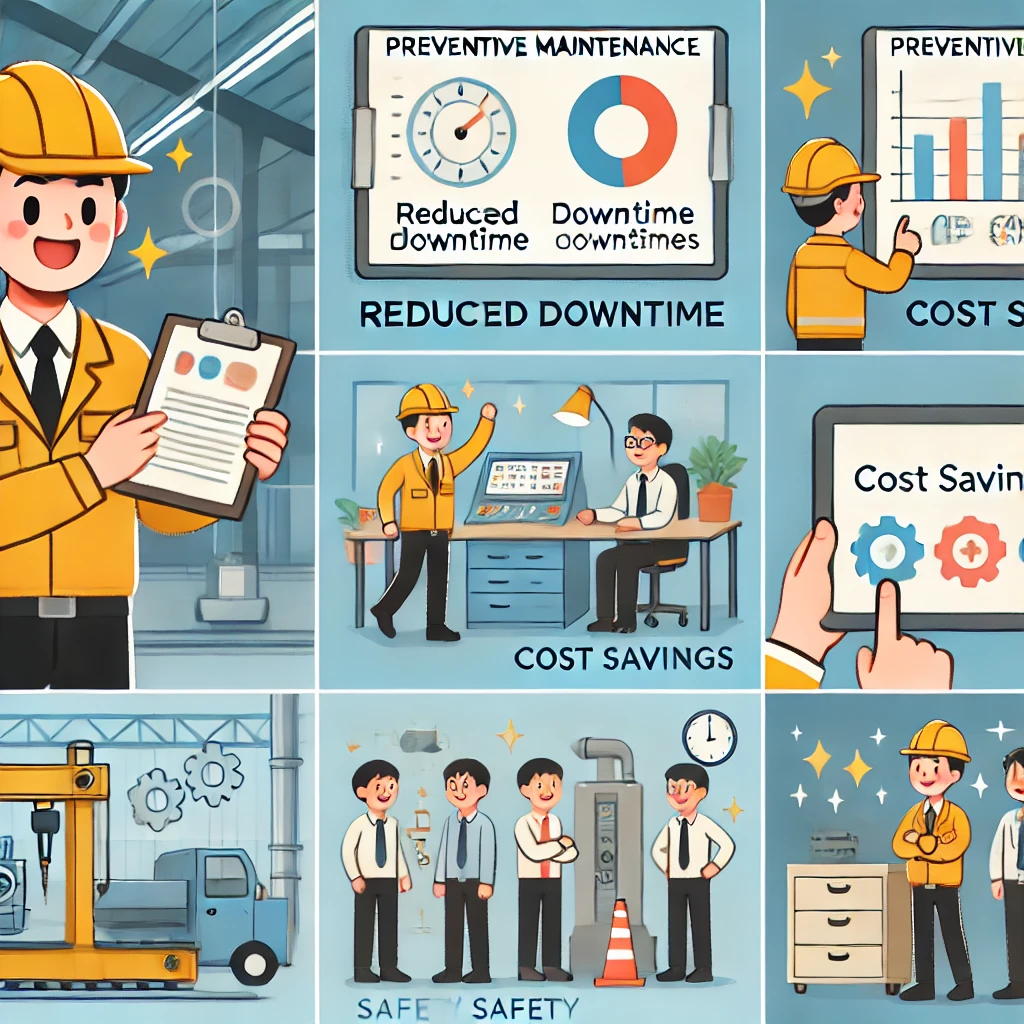
予防保全のデメリット
予防保全は、長期的な信頼性向上やコスト削減など多くのメリットをもたらしますが、その一方でオーバーメンテナンスや人件費増大、高額な導入費用などのデメリットも存在します。特に、センサー導入やAI解析による保全作業に取り組む場合には、初期投資やシステム運用コストを慎重に検討する必要があります。
また、メンテナンスのために生産ラインを停止させる計画管理は、業種や工場の生産体制によっては大きな課題となり得ます。これらのデメリットを最小限に抑えるには、設備の重要度や稼働状況を見極め、適切なタイミングと方法で保全を行うことが重要です。データ活用の精度を高め、過剰な交換や工数を減らす工夫をすることで、予防保全のメリットを最大化しながらデメリットを緩和できます。
5-1. オーバーメンテナンスのリスク
- 部品交換のタイミングが早すぎる可能性
設備や部品の寿命を正確に把握できていないと、本来まだ使用できるものを早々に交換してしまい、コストを増やす原因となります。 - 摩耗計測や状態診断の不十分さ
データ解析や状態監視技術が十分でない場合、過度に安全マージンを取りすぎて交換サイクルを短く設定しがちです。結果的に、部品の無駄遣いや廃棄量の増加につながります。 - 事例
例として、月単位で画一的に部品交換を行っている工場では、実際には負荷の少ない設備でも同様の頻度で交換するため、使える部品を捨ててしまう事態が生じることがあります。
5-2. メンテナンス工数・人件費の増大
- 定期点検のスケジュール化
設備の種類や数が多い場合、すべてを定期点検するための人員や時間が必要となり、運用上の負荷が高まります。 - 専門スタッフの必要性
設備の状態を正確に把握し、部品交換や修理が可能な技術者を育成・配置する必要があるため、人件費や教育コストが増加します。 - シフト計画や人材不足への対応
24時間稼働の工場や急な注文が多い業種では、メンテナンスに割ける時間が限られる場合もあります。保全要員のシフト組みや労働時間管理を徹底しなければ、過剰労働が発生する恐れがあります。
5-3. 導入・運用コストが高い場合がある
- センサーや監視システムの導入費
設備に取り付けるセンサー類、データ解析用のソフトウェア、ネットワーク環境整備など、導入時にまとまった資金が必要です。 - AI解析やビッグデータ管理のハードル
予知保全や状態基準保全に取り組む場合は、AIやビッグデータ解析の体制を整える必要があります。これには専門人材の採用・育成やクラウドサーバーの利用料など継続的なランニングコストが発生します。 - システムメンテナンス費用の増加
一度導入したシステムを長期的に安定稼働させるには、定期的なアップデートやバグ修正、センサーの校正などが欠かせません。新しい技術を取り入れるほど、こうした費用が上乗せされる場合があります。
5-4. 生産ライン停止の計画管理
- 生産ロスと納期遵守のバランス
メンテナンスが長引いたり、計画外のトラブルが発生したりすると、納期遅延のリスクが生じるため、事前の綿密なスケジューリングが欠かせません。 - メンテナンス時間の確保
点検や修理のために設備を一時停止するスケジュールを組まなければならず、生産効率への影響を最小限に抑える調整が求められます。 - 生産計画への影響
点検日や交換部品の到着状況と、製造ラインの稼働日程をうまく調和させる必要があり、需給変動の多い業種では難易度が高い場合があります。
予防保全の具体的な事例
6-1.製造業における定期点検
製造業の代表的な例として、機械加工を行う工場での定期点検が挙げられます。例えば、旋盤やフライス盤などの重要設備に対し、毎月の保守点検を決められた手順で行うことで、摩耗した部品の交換や異常の早期発見が可能になります。結果として、突発故障が減少し、生産ライン全体の稼働率が向上するのです。
また、自動車メーカーなどでは、ラインにセンサーを組み込み、機械の振動や温度を常時監視するシステムを導入しています。これにより、異常が見られた際にすぐメンテナンススタッフが対応できるため、不具合を未然に防ぎ、生産効率を維持することができます。
さらに、エアコンや冷却装置などの冷暖房設備についても、予防保全の一環として定期的な清掃やフィルター交換を実施することが重要です。フィルターの詰まりを防ぐだけでなく、機器全体の負荷を軽減し、エネルギー効率や設備寿命の向上といった効果も得られます。こうした定期点検の積み重ねが、企業の生産性とコスト面での優位性につながります。
6-2.食品業界の予知保全
ある大手食品メーカーでは、製造ライン上に複数のセンサーを配置し、温度や振動などのデータをリアルタイムで監視・分析しています。特に、冷蔵設備・加熱装置・混合機といった温度管理が重要な機器に対しては、細かな数値変化を捉えるためのシステムを整備し、故障の予兆をいち早く検知できる体制を構築しているのです。
- 故障発生前のメンテナンス
過去のデータから、温度や振動の変動パターンを学習・予測することで、一定条件下でのトラブル発生確率を高精度に算出します。その結果、ラインが停止する前に部品交換や調整を行い、重大なダウンタイムを回避しています。 - 品質・安全性の確保
食品業界においては、設備故障による生産停止だけでなく、異物混入や温度異常による食品品質低下が大きなリスクとなります。予知保全により設備状態を厳密に管理することで、製品の安全性と品質水準を保つことができ、顧客満足度の向上にも貢献しています。 - さらなる効果
得られたデータの蓄積と分析を活用して、稼働率向上やコスト削減といった生産効率の改善だけでなく、在庫管理や出荷計画の最適化など、サプライチェーン全体の見直しにもつながる可能性があります。
6-3.デジタル業界の予知保全
デジタル業界、とりわけ大規模なデータセンターでは、24時間365日の安定稼働が絶対条件となります。そのため、サーバーの温度・負荷・動作状態などをリアルタイムで監視し、故障前に異常を発見する予知保全の導入が進んでいます。
- センサー&ビッグデータ解析の活用
センサーから取得したデータを集約・分析し、過去の故障履歴と照らし合わせることで、異常発生のパターンを特定。わずかな温度上昇やファン回転数の変化なども見逃さず、先回りしてサーバーの負荷分散や交換対応ができるようになっています。 - ダウンタイム最小化とコスト効果
サーバー障害が起きると、サービス停止による顧客損失や信用低下が大きな痛手となります。予知保全によって故障リスクが高まる前にハードウェアを交換・修理することで、無駄なダウンタイムを大幅に削減し、運用コストの最適化にもつながっています。 - 経営全体への波及効果
予知保全の仕組みを導入することで、設備寿命が延び、追加導入・増設のタイミングをより計画的に管理できるようになります。結果的に、キャパシティプランニングやIT資産管理といった経営判断にも良い影響を及ぼし、ビジネスの拡大に対して柔軟に対応できるようになります。
これらの事例が示すように、予防保全はさまざまな業界で安定稼働と品質向上に大きく寄与しています。特に、食品やデジタルといった分野では、わずかなトラブルが致命的なダメージにつながる可能性があるため、センサーやAIなどを活用した予知保全がより一層注目を集めています。
自社に合った予防保全体制を構築するには、対象設備や業務特性を見極めたうえで、適切な手法を組み合わせることが重要です。今回紹介した事例を参考に、定期点検から高度な予知保全まで、さまざまなアプローチを検討し、企業競争力の強化につなげていきましょう。
IoTやAIの活用による予防保全の未来
近年、IoT(Internet of Things)やAI(人工知能)の技術が予防保全の手法に大きな変革をもたらしています。これらのテクノロジーを活用することで、センサーから取得した設備データをリアルタイムに解析し、異常の早期検知や故障リスクの事前把握が格段に容易になりました。具体的には、温度・振動・電流などの情報を常時監視するシステムを導入することで、通常では見逃しがちな細微な兆候を素早く捉え、突発的なダウンタイムを未然に回避できます。
さらに、AIは収集した膨大な稼働データや過去の故障履歴を学習し、将来の故障予測を行うことが可能です。たとえば、機械学習アルゴリズムを活用することで、「一定の条件下では部品摩耗が急速に進行する」といった傾向を見抜き、最適なメンテナンス時期を提案してくれます。これにより、部品交換や修理のタイミングを最適化し、必要最小限のコストで設備を良好な状態に保つことができます。
今後は、5Gやエッジコンピューティングなど通信基盤のさらなる発展に伴い、センサーからのデータをより高速・大容量で処理できるようになるため、予防保全の高度化は一層加速すると見込まれます。既に一部の先進企業では、設備や生産ラインを仮想空間に再現する「デジタルツイン」を活用し、稼働状況をシミュレーションすることで故障発生の確率や部品交換の必要性を可視化しています。こうした取り組みは、製造業だけにとどまらず、インフラ保全やエネルギー産業、医療機器のメンテナンスなど幅広い分野へも波及しつつあります。
このように、IoTとAIの進化により、予防保全の精度と効率は飛躍的に向上しています。企業にとっては、生産性向上やコスト削減だけでなく、信頼性の向上や安全性確保にも大きなメリットがあるでしょう。今後の製造業や設備管理の現場において、これらの先端技術は競争力を左右する重要な要素としてますます注目を集めるはずです。
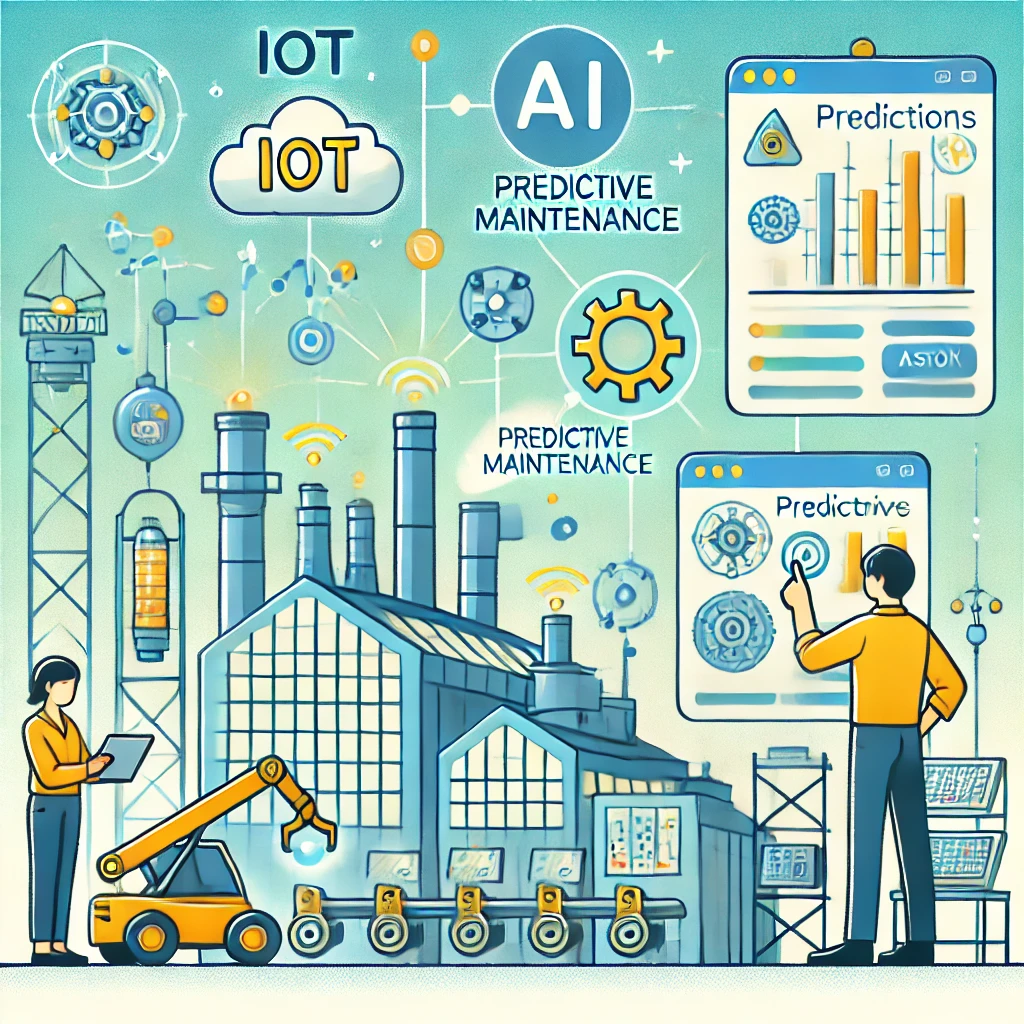
まとめ
予防保全は、生産設備の安定稼働を支える極めて重要な手法です。定期的な点検やメンテナンスを行うことで、機器故障のリスクを最小限に抑え、突発的な生産停止を防ぐことが可能になります。これにより、効率的な生産体制と高い稼働率を維持できるだけでなく、企業全体の信頼性やブランド価値の向上にも寄与します。
もっとも、予防保全にはスケジュール管理や設備の一時停止など、短期的な負担が増える側面も存在します。しかし、長期的に見ればトータルコストの削減や持続的な運用が実現できる可能性が高く、企業にとって投資する価値は十分にあると言えます。
結論として、予防保全は製造業や設備管理に不可欠な要素です。自社の運用状況や設備特性を踏まえ、最適なアプローチを検討・導入することで、トラブルの軽減やコスト効率の向上を図り、安定した生産活動と競争力強化につなげていくことが望まれます。